Benefits Of and How to Color-Code in Your Facility
Color-coding is an effective way to minimize cross-contamination and other hazards within a sanitary processing facility. Although it is not yet a requirement, color-coding can demonstrate a company’s dedication to the quality and consistency of their products. From beverage to dairy, pharmaceutical to food processing, color-coding helps maintain a high level of safety for both their employees and end-consumers.
COLOR-CODING CAN BE PARTICULARLY HELPFUL FOR:
- Maintaining strict work zones
- Reducing the risk of pathogens and allergens that can be harmful to your sanitary process
- Eliminating other foreign contaminants from affecting your operation
- Minimizing miscommunication throughout a facility’s processes
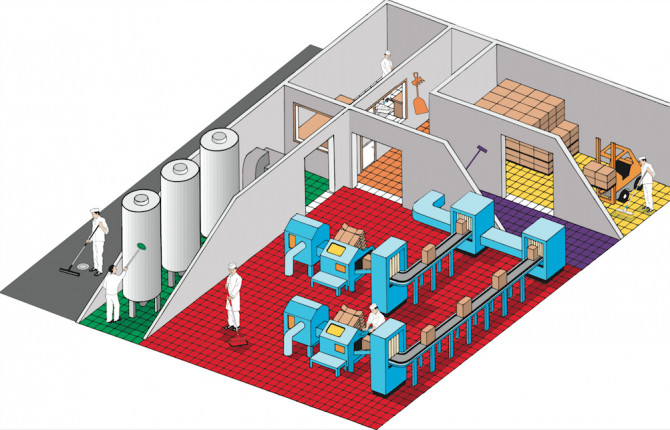
Is Color-Coding Right for your Processing System?
Now that you understand the different ways to apply color-coding in your plant, let’s find out if there is a need for color coding in your facility! A number of factors influence the decision to implement this system. To decide if color-coding is right for your processing facility, consider the below criteria:
- Does your plant process food, dairy, beverage or other consumable products?
- Do any of the ingredients used in the food production process pose microbiological threats?
- Do your cleaning agents or chemicals in any area pose a threat if transferred to another area?
- Is it necessary to separate tools based on the areas where they are used, such as equipment vs. floors and drains, or food contact vs. non-food contact areas?
- Does your facility process foods that contain ingredients that are known as common allergens, such as milk, eggs, fish, crustacean shellfish, tree nuts, peanuts, wheat or soy beans?
- Does your facility maintain a HACCP plan or a master sanitation schedule?
- Does your plant utilize a 5S System?
- Do you have separate manufacturing lines for different products?
- Do you have a need within your plant to divide work spaces in order to maintain quality control?
- Do you have manufacturing processes that must be consistent from facility to facility?
- Does the FDA or USDA have regulatory authority over your products or provide input into your process?
- As a US-based processor, do you have employees who do not speak English as their native language?
- Do you have issues with tools being misplaced or used inappropriately?
- Is your facility required to meet certain sanitation standards?
If you answered YES to any of the above questions, your processing plant is a strong candidate for color-coding!
4 Ways to Apply Color-Coding in Your Plant
- Use to distinguish cleaning versus sanitation in your maintenance routines. For example, “Black” is a common color used to identify cleaning tools used for floors and drains. Select other colors to designate tools that are to be used for sanitizing food contact surfaces, or designate tools that are specified for use with certain chemicals. This can help prevent the occurrence of using an unsuitable cleaner on the wrong processing equipment.
- Implement color-coding to provide “zone control.” Assign different colors to each step in the process or by manufacturing line, whichever makes sense in your facility. When colors are assigned to zones, confirming that a tool is misplaced is simple, and tracing it back to its point of origination is fast. This level of traceability can translate to the prevention of costly recalls.
- Designate workspaces, even when ‘’zoning” isn’t applicable, such as color-coding for particular shifts. This is particularly helpful to companies that closely monitor tool and equipment costs. This type of color coding can help in reducing incidence or misuse of tools in unapproved areas, as well as fewer lost or misplaced items.
- Reduce waste and optimize productivity by using color-coding as part of your 5S System. This method of color-coding promotes a workplace culture where tools and supplies are placed where they are needed and well maintained for longevity of use. Once you have determined that your facility would like to implement color-coding, it is important to take the time to plan a system that makes sense for you. Each plant and facility is different, but here are some tips to get started.
1. KEEP IT SIMPLE!
Once you have identified the hazards that can benefit from color-coding, be sure to keep your color assignments logical and as simple as possible. An easy rule to follow is to assign only ONE color per zone and ensure that the colors make sense in relation to your process. Additionally, double check the availability of colors in the tools you need before finalizing plans. A Rodem representative can check availability.
2. BE CONSISTENT!
The next step after you have made logical color assignments is to consider where the color should be applied to guarantee the process is properly followed. Key items within a particular Critical Control Point or zone should be identified with the appropriate color to assure consistency. This allows you to easily determine when color-coded work items have been misplaced and items can be tracked with greater ease. Make sure your documentation at each point of use is also consistent with the paperwork used by your purchasing department or quality manager.
3. COMMUNICATE THE PROGRAM!
How you are going to communicate the program rollout to employees is just as important as deciding to implement and carefully planning your program! The best way to communicate the implementation is to use your facilities existing guidelines for how to communicate changes. Be sure to meet with your shift employees, include details about your color-coding program in GMP’s or other documentation and implement company wide. It is not a best practice to have one part of the plant operating on old procedures, while the other part is using the new color-coded program.
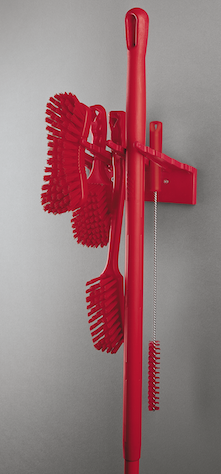
In conclusion, color-coding at your sanitary processing plant is a great way to reduce hazards and avoid cross-contamination. As you can see there are a number of ways to use this program in your facility. Be proactive and show your dedication to high quality and consistency of products while maintaining a high level of safety for both end users and employees.
Contact us to enlist the help of a pro from Rodem to help determine how to make color-coding work best for you.
**Special thank you to our manufacturing partner Remco Products for providing us with the info for this article that has been adapted from their original. Download Remco Products whitepapers here. Remco and Vikan® brands offer the most tools in the most colors for flexibility in designing comprehensive color-coding systems. Call Rodem for more info on Remco Products.**