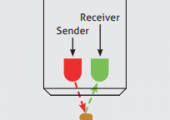
What Is a Turbidity Meter & How Does It Work?
Learn about how exactly a turbidity meter works, the benefits it offers, and why it might be the perfect solution for your sanitary processing applications.
Turbidity measurement is an crucial parameter for the automation of many processes. Anderson-Negele offers hygienic turbidity sensors for almost every application.
The inline analysis of media based on their turbidity values enables automated, high-precision application in many production processes and application areas. These are primarily product differentiation, phase separation, process control and quality monitoring.
In a variety of processes and CIP systems in dairies, breweries, the beverage industry, wine production, juice production and other food companies, turbidity sensors can measure liquids according to qualitative criteria in real-time and fully automatically. This give processors the ability to:
Minimize the loss of raw material
Less cost for waste water treatment
Ensures high quality of the product
Efficient separator control
Modular flush turbidity sensor for low to high turbidities 200…300,000 NTU, with IO-Link.
Ideal for e.g. phase separation, yeast harvesting, CIP return control.
For very low turbidities 0…5,000 NTU, for pipes from DN25. Ideal for e.g. efficiency improvement in separator automation, lauter tun and filter monitoring. Water management e.g. fresh and waste water control.
For very low turbidities 0…5,000 NTU, for pipes from DN25. Certified for water management e.g. fresh and waste water control.
Rodem specialized in custom sanitary process fabrications and solutions. Discuss your full project needs with a Rodem team member to see how we can help you build the exact system you need.
Learn about how exactly a turbidity meter works, the benefits it offers, and why it might be the perfect solution for your sanitary processing applications.
When a customer approached Rodem with a desire to reduce the amount of waste during changeover, our engineers designed a system that eliminated the waste and sped up changeovers at their fillers. Learn more about how Rodem solved this unique problem.
Continually dwindling profit margins faces producers year after year and the need to reduce product waste continues to be a reality. See how the Anderson ITM-3 can help cut your product waste and add to your bottom line.
A large Dairy was able to cut its CIP consumable costs by 20% in the first 90 days of use when they installed an Anderson-Negele ITM-3 Turbidity Sensor to monitor CIP rinse water in their system. Learn more about how this product works and find out how it can help you cut your CIP consumable cost.
E-mail: [email protected]
Copyright 2024 Rodem Inc. All rights reserved.