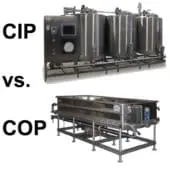
CIP vs. COP: Which is Right for Your Facility
If you are considering enhancing or introducing CIP or COP procedures or equipment into your plant it is vital to have a complete understanding in order to take full advantage of these processes.
Office Phone: 800-543-7312 Ext. 148
Email: [email protected]
Prior to joining Rodem in 2012, Kevin Trauth served as the Plant Engineer and Assistant Plant Manager at his family-run business, Louis Trauth Dairy/Dean Foods. Having grown up in the dairy industry, Kevin’s wealth of knowledge on sanitary processing combined with end-user experience provides him with a unique perspective and understanding of the challenges unique to the product, facility and staff for each project. When Kevin’s not thinking about processing, he enjoys being outdoors, classic cars, and spending time with family.If you are considering enhancing or introducing CIP or COP procedures or equipment into your plant it is vital to have a complete understanding in order to take full advantage of these processes.
When a customer approached Rodem with a desire to reduce the amount of waste during changeover, our engineers designed a system that eliminated the waste and sped up changeovers at their fillers. Learn more about how Rodem solved this unique problem.
Don’t let missing parts halt production. Rodem offers same-day shipping on stainless steel fittings from one of our four stocking locations. Learn more.
Don’t sacrifice quality for cost. Learn more about the Alfa Laval Unique Mixproof CP-3 Valve and how it compares to the competition.
Reduce downtime and decrease strain on resources with Alfa Laval Gamajet products. Learn more about achieving safety, sustainability and cost savings with tank cleaning optimization from Rodem.
The Rodem team successfully executed the design, build and install for a dairy and ice cream producer to bring their system up to date and improve throughput.
Is it time to upgrade your CIP system? See the key factors in deteriming between a single use system versus a reuse system to help determine the best fit for your sanitary process.
Alfa Laval’s sanitary processing equipment is designed to keep up with the demands of the growing food industry. Learn more about optimizing your process with Alfa Laval products.
Have you been burned in the past by specifying the wrong size for your check ball orders? This list allows you to compare manufacturer reference sizes to the actual OD and find the size you need.
For Sanitary Producers, preventing unwanted microorganisms and dangerous recalls are of utmost importance. Learn how orbital welding can prevent these issues, while increasing productivity and safety!
A custom designed multi-valve bio-block solution was the ticket to cleaning up a messy valve skid for this international pharma producer. Is a custom solution right for you?
Manual tank cleaning is not only time consuming, but is proven to be only a semi-reliable method. Investing in an automatic tank cleaning has many benefits such as using less water and reducing the time spent on cleaning.
Good Manufacturing Practices (GMPs) are practices and procedures performed by food manufacturers, which play a critical role in ensuring food safety. Use this checklist to ensure you’re in compliance!
Sanitary processing companies are well aware of the regulations and policies in their businesses. In order to reduce contamination loss, companies need to stay ahead of the ever-evolving sanitation rules and regulations in the industries they serve, especially in their equipment.
Considering the viscosity and adhesion of tomato juices and pastes, cleaning the large number of sanitary processing equipment they come in contact with is not an easy prospect. Learn the Rodem solution!
A large Dairy was able to cut its CIP consumable costs by 20% in the first 90 days of use when they installed an Anderson-Negele ITM-3 Turbidity Sensor to monitor CIP rinse water in their system. Learn more about how this product works and find out how it can help you cut your CIP consumable cost.
The FDA has been working with growers, processors, and suppliers, in their hopes to assume a more preventative role through the Food Safety Modernization Act. Learn what this act means for your food processing facility, and what measures you can take to ensure you’re meeting the proper guidelines.
Rodem’s extensive inventory and experienced customer service representatives were able to provide critical spares to a major Midwest pharmaceutical producer over the weekend to ensure the plant was up and producing on Monday.
Increased food safety regulations are generating a need for well documented food safety management systems in food processing plants. One tool processors have access to help them in the management of food safety risks is color-coding.
A simple switch from plastic to rubber rotors helped a Midwest Dairy customer realize an estimated 1st year savings of $20,000+. Check out the table below for hard savings specifics.
“Dan was the only one of multiple US based providers to come through with valves and pumps to re-fit Castlebar.”